This paper was the subject of a presentation at the AGS Safety in Mind conference in November 2019, and started by asking “why this subject, and why now?”. During a prior AGS Safety Working Group meeting, we had debated whether the Health & Safety Executive approve or agree with the AGS guidance notes? In particular we debated whether common UK trial pitting methodologies complied with the Work at Height regulations 2005; and specifically, we were interested whether the common practice of standing or kneeling close to the edge of an unprotected trial pit, 2,3,4m+ deep might be deemed in hindsight to not comply with the law. The purpose of the presentation was to raise awareness of the issue to younger practitioners, remind senior practitioners and managers of their duties, to promote debate about the sufficiency of current industry practice, and debate whether current practice meets the legal benchmark of good practice.
There are a number of hazards associated with trial pits, although used generally safely for many decades. The Work at Height Regulations 2005 clearly apply to this work, and place legal duties on employers. Very few practitioners have ever experienced an incident involving a fall into a pit. Nevertheless, we have the opportunity to consider whether we should or could do more to manage the risk from working at height adjacent to unprotected trial pit edges. The time to have this debate clearly is not when a HSE inspector is questioning you following a serious accident, but preferably by industry collectively and in advance of such an incident ever occurring.
I have been involved in trial pitting since the 1980s, and have learned much about the ground from being up close, which a trial pit allows. My experience of trial pits is that it can be dirty, tiring, and potentially hazardous work. However, they are often fun, provide good information and experience, and sometimes are even a fabulous day out. They are economical, quick to organise, undertake and report.
Conventional machine dug trial pits expose the logging engineer to an unprotected edge of potentially 3 to 4 m depth in order to undertake at least part of their task. This Introduces a risk of becoming unbalanced or tripping at the edge whilst observing, taking measurements, sampling or photography. In my 30 years’ experience I am not aware of a logging engineer falling into a trial pit. A questionnaire survey sent out to AGS members in summer 2019 also concluded that there is no knowledge within the membership of falling into trial pits, although we subsequently became aware of anecdotal experience of 1 non-injury fall into a pit filled with groundwater! Whilst we know that trial pit faces can collapse and whilst it is theoretically possible for such a collapse to involve the logging engineer, experience over a substantial period of time shows us that logging engineers don’t fall into trial pits, and therefore the proven probability is extremely low to negligible.
However, probability is not the only component of risk, severity of consequence also has to be considered. The consequence of falling two, three or 4 m into a trial pit is likely to be severe, it is likely to involve broken bones, a broken neck or worse. Using typical industry risk assessments, a combination of low or very low probability along with medium to high, to very high consequence generates a medium to high, to very high risk. The risk is significant, such that measures need to be considered to mitigate it.
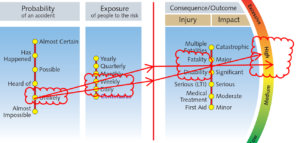
“SFARP” and the Work at Height Regulations
Regulation 6 of the Work at Height Regulations 2005 is titled “avoidance of risks from work at height”. It describes a hierarchy which employers are required to work through and give consideration to when planning work at height, requiring at each level a consideration as to whether the available controls reduce the risk “so far as reasonably practicable” before discounting a control and using a lesser control.
But what is the required level of the duty of “so far as is reasonably practicable” – how does an employer know how far they need to go? The HSE guide “Working at height: a brief guide” states that “low risk relatively straightforward tasks will require less effort.” They go on to say that “there will also be situations where common sense tells you no particular precautions are necessary “. Whilst this does not provide any specific guidance in relation to trial pits, it does acknowledge low risk situations (albeit not necessarily low probability situations). By extension, higher risk situations require greater controls.
Case law in respect of SFARP leads us to Edwards v National Coal Board 1949, which established the principle that the quantum of risk is placed on one side and the sacrifice whether in money, time or trouble involved on the other. If it can be shown that there is gross disproportion between them, the duty has been discharged.
So where is trial pitting practice in the 21st-century in relation to SFARP – does it pass “the gross disproportion” test? HSE suggest in their report “Reducing Risk Protecting People” (“R2P2”) 2001 that they regard a risk as not significant if past experience shows the risk to be extremely low (note “risk” not probability). HSE also state that they would consider sources of good practice, standards or guidance agreed by bodies representing industry. They would consider an assessment of the extent to which the practices have achieved general acceptance, and they will decide whether adoption of any authoritative good practice precautions is an adequate response to the hazards. HSE then say that “in most cases adopting good practice ensures that risks are effectively controlled”.
However, HSE go on to say that a universal practice in industry may not necessarily be good practice or reduce the risk sufficiently; they make it clear that duty holders should not assume that it is. They state that there will be times when existing practice is found to result in inadequate control of risks. So, we come to the question which opened this presentation: is current industry guidance, including AGS guidance on trial pitting and working at height, representative of good practice such that the HSE would consider it as an adequate control of the risks?
The AGS Trial Pitting Survey 2019
In order to get a better understanding of modern common practice, the AGS Safety Working Group circulated a questionnaire to the membership in summer 2019. The main outcomes were summarised at the 2019 conference, and key headlines repeated hereafter.
TOPIC |
INDUSTRY RESPONSES |
Guidance used when planning trial pitting |
Most respondents stated they use the current AGS trial pitting guidance, and a number stated they have in-house / company guidance of some kind.
Several respondents suggested that they refer to BS5930 although there is only limited safety guidance there. A number of respondents refer to HSE “working at height a brief guide” and HSE CIS614 Excavations, although neither of these provide much useful guidance in relation to trial pits.
No respondents identified the existing AGS guidance on Working at Height as informing their working arrangements. |
Competence to work near an unprotected trial pit edge |
Almost all respondents had some form of assessment of competency and a period of supervised handholding typically 3 to 6 months.
Some have in-house trial pitting and work at height awareness elements of training
Many use CITB SMSTS or similar.
Most use CSCS, however usually not on its own. |
How duty holders address the hierarchy of controls in Regulation 6. |
Many respondents prevent access anywhere near the trial pit by other workers
The vast majority do not make use of protection such as barriers or fall prevention/protection using harnesses, mostly on the grounds of perceived or experienced impracticability.
Some practitioners have tried to use mobile barriers, staging boards, fall protection harnesses
Some practitioners try not to use trial pits.
Some practitioners leave the JCB bucket in the hole to reduce height of fall. |
Demonstration of SFARP at each level of the hierarchy, for example by considering risk against cost and benefit. |
No respondent stated that they undertook such a specific assessment
Some respondents believe that SFARP was embedded in their company work procedures and training of staff, the use of risk assessments, method statements and CDM design risk assessments, and through following AGS and HSE guidance documents. |
Reasons why control measures are considered to be SFARP
|
Some respondents suggested that they do not provide fall protection for walking down a flight of stairs, where there is clearly a fall hazard of a highly frequent nature, and potentially just as severe as a fall into a trial pit perhaps.
Respondents said that the staff are aware of the risk of falls into trial pits, and they have the ability to stop work if they consider it unsafe.
Some respondents referred to the HSE guidance which flags up that there are some low risk solutions which suggests precautions may be unnecessary. |
It would appear that a specific consideration of SFARP / gross disproportion is not an adopted basis of decision-making within the industry. Note however that it is not a legal duty to demonstrate SFARP, it’s just a legal requirement to be SFARP. Many respondents referred to the very low probability of an incident. Comments included “ … falls from height incidents in company history were zero …”; that “… there is not a great deal of empirical evidence to say there is a recognised pattern or trend of significant danger of falls…”; and a number of respondents stated that in circa 20 to 30+ years, they have never encountered nor heard of any injury from falling into a trial pit. Finally, many respondents reiterated that trial pitting is an essential method of investigating the ground.
The questionnaire responses presented a widespread belief throughout industry that other potential methods such as barriers and harnesses, even remote tools, were impracticable on the basis of cost, the introduction of other more prevalent hazards and risks, and the maintenance and inspection requirements and training. Many respondents believe that such measures are not necessary nor appropriate, given the very short duration of a trial pit.
Finally, respondents were asked what additional controls they would consider adopting if it could be achieved practicably. Responses included “… a safe excavation cover…” ; “… a barrier that was lightweight, affordable and practicable, which could be used to protect up to the edge or even over the excavation …” ; “… extendable trial pit covers …”; “… purpose designed lightweight edge protection barrier system …”; “… an open lattice to prevent a fall to no more than ground level …”; “ … a standard type of barrier system, aluminium, easily folded up and deployed”.
Tolerability of Risk
We’ve noted the potential and the risk of a fall, looked at the law and guidance, and at a subset of industry views on trial pitting. Does it help us determine whether current practice is good practice, and whether we need to be doing more?
Perhaps instead we can ask ourselves: “Can we tolerate the consequence of a fall?” HSE state (“R2P2”) that “tolerability does not mean acceptability. It refers to the willingness to live with a risk to secure benefits, in the confidence that it is being properly controlled. This means that we do not regard it is negligible or something we might ignore rather as something we need to keep under review and reduced to further if and as when we can”. And that is the point of this initiative from AGS: to keep our measures under review.
Were one to examine the adopted common controls against the levels of the Regulation 6 hierarchy, we see the majority of our current controls sit very close to the bottom of the hierarchy, and particularly in the “others” category. There is a noticeable gap the within the “prevention of falls” and also the “Minimising the distance and consequence of falls” levels, conventionally those areas where other industries focus their controls.
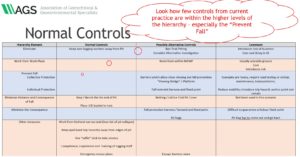
Over the past decade at least, various practitioners have experimented with the use of harnesses to some fixed point, and staging boards with fixed scaffold barriers to view trial pits from, and encountered impracticability’s, not least the consequent and guaranteed introduction of a number of other risks which are more likely to cause an injury.
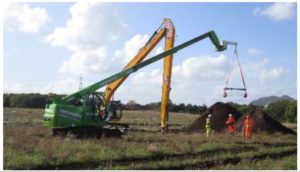
However, using the benefits of modern innovations that are now available to the market, there are products which are beginning to be used in the construction industry to minimise fall distances in particular, and whose prime benefit is that they are lightweight and portable. AGS would be very interested to gain feedback of the use of such equipment for trial pitting.
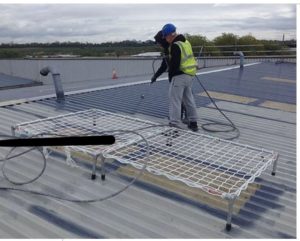
In conclusion, trial pits are immensely valuable to good ground engineering. Much of that only comes from seeing first hand into the pit from close up; that involves approaching the edge and crouching down; it allows the taking of well composed photographs of features that you only see because you can look inside. The time of exposure to risk, and the probability of falling into a trial pit when logging is low to very low and possibly unheard-of. However, the consequence of a fall is probably serious injury or even fatality, certainly life changing. If we wish to continue to use trial pits:
- ethically we should only specify them when we are really going to make proper use of them
- we should continue to look to use modern technology to improve our protection from falls from height.
- we should think more about emergency arrangements (including a rescue plan), in advance of when we need them.
AGS are establishing a trial pitting subgroup of the Safety Working Group and would be interested to hear your experiences, viewpoints or potential involvement.
References
- https://www.ags.org.uk/content/uploads/2019/11/Working-at-Height-during-trial-pitting.-How-far-is-So-far-as-is-reasonably-practicable-Steve-Everton-Jacobs.pdf
- The Work at Height Regulations 2005 http://www.legislation.gov.uk/uksi/2005/735/contents/made
- HSE 2014 Working at Height :a Brief Guide. INDG401 Rev 2 https://www.hse.gov.uk/pubns/indg401.pdf
- https://www.hse.gov.uk/construction/safetytopics/excavations.htm
- https://www.hse.gov.uk/pubns/cis64.pdf
- https://www.ags.org.uk/item/ags-guidance-for-the-safe-excavation-of-trial-pits/
- https://www.ags.org.uk/item/guidance-on-work-at-height/
- Reducing Risk, Protecting People (R2P2) HSE Books https://www.hse.gov.uk/risk/theory/r2p2.pdf
- Edwards v National Coal Board [1949] 1 KB 704; CA [1949] 1 All ER 743
Photo Acknowledgements
Oxford Safety Components Ltd; Structural Soils Ltd; Jacobs; BAMRitchies;
Article provided by Steve Everton, Jacobs, CEng MICE, Construction Health & Safety Registered (Advanced)