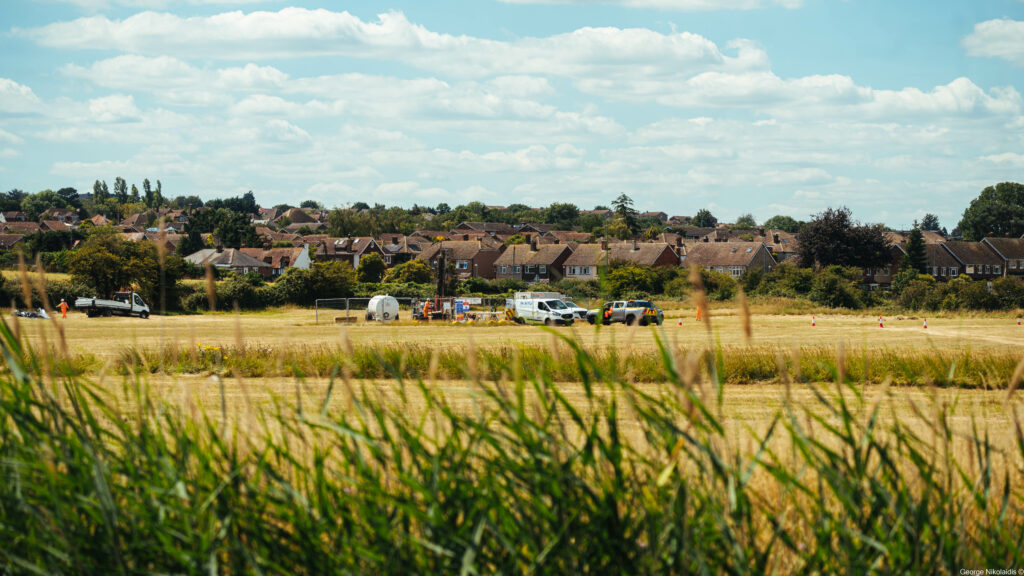
Article contributed by Patrick Cox. Managing Director for Environmental Contracting, AECOM and Dr Emma Langman, Managing Partner of BakerFish
The Lower Thames Crossing is described as ‘the biggest road project’ since the M25’. It’s also set to become the third-largest bored tunnel in the world, being built under the river in the heart of one of the world’s busiest cities. It needs to be right!
The client, Highways England needed to ensure that all the data necessary regarding ground conditions and wider environmental considerations be available to ensure that the project is designed and built safely, efficiently, and with care to protect the natural and human environments.
Perfect Circle Joint Venture (a unique partnership between Pick Everard, Gleeds and AECOM) was appointed through the SCAPE framework to carry out multiple phases of the ground investigation work required.
Phase 3 began in early 2021, just as news began to emerge of the new Coronavirus threat. The same month that the country went into lockdown, Perfect Circle appointed BakerFish as their Lean Consultant.
Does Lean apply to Ground Investigations? We are different!
Managing Partner, Dr Emma Langman explains:
“In 20 years of working with organisations to apply Lean principles, I have never yet come across one that didn’t claim to be ‘different’ and ‘unique’ and that Lean – with it’s background in manufacturing’ would “not work here.
“The ground investigation sector is no exception to this rule of thumb.
“I remember going head-to-head with one of the leadership team and saying ‘listen – if Lean can work on the oil fields of Iraq, it can certainly work in a farmer’s field in Essex’
“It was one of those moments when a consultant holds their breath to see what will happen. But I knew that Patrick and his team were fully committed to creating a culture of Lean and delivering efficiencies for Highways England, so it didn’t feel too risky to challenge.
“At the end of the day Lean only works when leaders engage and lead it. And in this project they certainly did”.
When you consider the nature of ground investigations, they are “not standard engineering” Emma explains, rather they are “huge open air science experiments, with large samples of soil rather than small samples of chemicals in test tubes”.
In fact, over the course of the Lean intervention, the entire team appreciated that ground investigations are about the flow of data – not of soil!
Did you really become more efficient because of Lean?
Recognising that GI is all about the flow of data through a system, the team used Lean principles to implement some huge savings for their client.
Managing Director, Patrick Cox gives an interesting example of how changing thinking towards a Lean mindset can have incredible results for a tiny investment in this anecdote:
“Before Emma joined the team we had done a lot of ‘common sense’ improvements, which we later learned were examples of Lean Thinking.
“For example, my team went to visit the laboratories in our supply chain to look at best practice for laying out logging and testing facilities. From this we decided to create a shared logging facility that was specifically designed to provide a number of benefits including protecting our team from bad weather, enabling digital labelling and tracking of samples, providing a controlled environment for sample storage and more.
“This had already achieved savings in the hundreds of thousands of pounds, as well as driving up consistent and efficient ways of working to ensure quality and value for money.
“Even so, towards the peak of the ground investigation fieldwork we found that the logging facility was being swamped by samples for processing.
“Under pressure we slipped back into conventional thinking patterns and considered the solution to running out of space was obvious – increase the space!
“However, the costs of renting more facility space would come at a heavy cost.
“Instead, Emma nudged us on the call to remember that Lean is all about flow and that GI is all about data.
“So keeping front of mind that Lean is about reducing variation and waste, the answer became obvious. Instead of procuring more space we simply arranged for more frequent ‘drop-offs’ of sample, which ‘smoothed the flow’ through the logging facility, flattening the demands curve, and meant that we saved the cost and effort of extending the facility.
What about improvements in the field?
Again, since GI work is essentially ‘a giant outdoor science experiment’ it is a great candidate for Lean improvement. The team used tools like TIMWOOD, root cause analysis, the 5 Whys (where you literally ask Why? 5 times) to find a number of improvements. For example, using our partner Equipe to undertake audits on machinery before it was used helped to avoid breakdowns, as well as (most important of all) improving the safety of the workforce.
In Package C, which hosted the Highways England site visit for their lean assessment (Simplified Lean Capability Assessment) the assessors were delighted to see how rig-side layouts were standardised and value-enabling work (such as setting up and taking down fencing etc) were provided by a support team, leaving the highly specialised rig teams free to focus on the ‘value-adding’ work of drilling.
What did the client think of your efforts in Lean?
The Simplified Lean Capability Assessment undertaken by Highways England scored an impressive 3.3 out of 4 (where 4 is ‘world class’ such as Toyota).
What are the key lessons for our readers?
Patrick shares “I was genuinely surprised to see the extent that Lean is applicable to GI work. It was great to be able to deliver several million pounds worth of efficiency savings to our client while still achieving the project goals and collecting high quality data for the Lower Thames Crossing. Lean was key to that saving being realised”.
Emma says “it’s all about leadership. The Perfect Circle team really led from the top and over 30 managers (including several of the senior leadership team) engaged in one-to-one coaching to help them take on this new way of thinking. It was also great to see the high levels of partnership working between Perfect Circle and their client team LTC, and Highways England, as well as the enthusiasm and engagement of the specialist suppliers involved in the project. In twenty years of working in Lean, this was the most ‘joined up’ working and commitment to efficiency and quality I have seen. And that starts from the top”.
For more information and details including 40 different case studies of how Lean improved this project, please contact Patrick.Cox@aecom.com or emma@bakerfish.com.
And, last but not least, if you would like to learn more about the leadership that makes Lean work, take advantage of this offer for AGS readers who can claim a 10% reduction in ticket fees for the Servant Leadership Conference in May 2021. Find out more at www.servantleadershipconference.com and claim your discount using the code: AGSdisc10.