Trial pitting and trial trenching have long been a popular investigation tool within the geotechnical and geo-environmental industry. Trial pits and trial trenches are commonly specified in both geotechnical and geo-environmental investigations and are often a preferred investigative method to enable a rapid check of the condition of the ground. They permit examination of both horizontal and vertical faces exposed as the pit is advanced and also enable the collection of a wide variety of sample sizes and types. Trial pitting and trenching is commonly undertaken using a machine excavator, whether this be a backhoe excavator or a tracked 360 machine. For shallower excavations, or where trenches are required to provide more detailed interpretation of the stratigraphy or underground service identification and mapping, these are often undertaken by hand with or without machine assistance. Vac-Ex technology has also been used by the industry to excavate trial pits and trenches.
Trial pitting is seen as an economically advantageous investigation tool which enables a fair spread of exploratory points to be undertaken within a typical working day. In addition, trial pitting facilitates a wide variety of in-situ tests, for example Hand Shear Vanes, California Bearing Ratio (CBR) tests, Plate Load tests and Infiltration tests in accordance with Building Research Establishment (BRE) Digest 365 Publication (2016).
With a better awareness of health and safety risk within our industry over the past decade or so should we not, however, ask the question whether trial pitting is still fit for purpose and therefore should we strive for an alternative method?
Health & Safety law often uses the term, “so far as is reasonably practicable (SFARP)” forming the basis of any risk-based activity and as such must be used as a decision tool on the risk against the cost and availability of technology to control it. The HSE, in investigation and prosecution, make a computation in which the quantum of risk is placed on one scale and compared with the sacrifice involved in the measures necessary for averting the risk (whether in money, time or trouble) on the other scale. The legal test would be that measures which are disproportionate (or grossly disproportionate) would not be SFARP.
All trial pitting activities including site preparation, excavation, sampling, logging and backfilling must be planned and a suitable and sufficient site-specific risk assessment made, contributing then to a method statement. However, consider this: with the Work at Height Regulations (2005), any excavation which has the potential for a person to fall is classed as working from height and, therefore, requires measures to be put in place in accordance with a specified hierarchy (while considering “SFARP”) to comply. Whilst injury can be caused from a fall from any height, a trial pit which is excavated to depths often in excess of 3m can pose a significant risk of injury should an operative fall into the excavation.
Additionally, the Construction Design and Management (CDM) Regulations (2015) were amended and now identify ground investigation as an integral part of the construction activities. Trial pitting as an activity is covered under Regulation 22 (Part 2) which states that “Suitable and sufficient steps must be taken to prevent any person, work equipment, or any accumulation of material from falling into any excavation”.
Furthermore, Regulation 22 (Part 1) of the CDM Regulation states that “All practicable steps must be taken to prevent danger to any person, including, where necessary, the provision of supports or battering, to ensure that; no excavation or part of an excavation collapses; no material forming the walls or roof of, or adjacent to, any excavation is dislodged or falls; and no person is buried or trapped in an excavation by material which is dislodged or falls”.
Therefore, all excavations require an assessment to be made of the stability of the excavation prior to commencing the dig and during the dig. These risk assessments should consider factors such as influence of the excavation method, ground conditions, buried services, obstructions, groundwater level, water strikes, contamination etc. An initial risk assessment can be produced to reflect the general approach but inevitably the trial pitting supervisor/logger will need to carry out dynamic, sometimes called “point of work”, risk assessments and where these necessitate or identify significant changes to the risk or methodology it should be documented.
However, as trial pitting work is often undertaken by graduates or technicians, can employers be sure that these individuals possess the required knowledge, training and experience to meet sufficient competency requirements or have the ability to make these assessments and informed decisions?
When detailed logging (i.e. service identification, detailed fabric logging, scan lines or assessment of slip planes) is required, due consideration should be taken to the necessity of entering the trial pit/trench. Where the designer determines that entry is essential, the Contractor must ensure that the excavations are sufficiently shored or the excavation sides battered back or benched to reduce the height of exposed material and potential collapse. Due consideration should also be taken by the Client to allow sufficient time and resources (money) to develop this safe system of work, to carry out any additional training requirements and for the actual work. In addition, these type of trial pits should be located to provide sufficient working room for the plant which will be required for the installation and maintenance of the support system and spoil. As these types of works may be of a longer duration than typical trial pits, physical barriers such as fencing may be required which adds additional costs and time.
When trial pits are part of a more typical ground investigation and require standard logging, in-situ testing and sampling the designer and contractor should consider carefully whether any entry is required whatever the depth. The AGS promotes an approach which does not require entry and therefore, the risk of injury through collapse and subsequent burial is reduced. However, this does not eliminate totally the risk of working at height.
With trial pitting seen as a relatively quick and cost-effective method of ground investigation, the use of edge protection and trench support can be viewed as unrealistically costly and time consuming to install. Compliance with the hierarchy of controls within the Work at Height regulations might suggest to some employers that installation of edge protection or a suitable fall arrest system or other safe system of work, should be mandatory for all excavations. However, the main advantage of trial pitting is to provide a quick and easy way to view the stratigraphy and close up inspection of the pit is necessary to obtain the desired results. Judgements on the required controls under the Work at Height regulations are however to be determined “SFARP”.
The current AGS Guidance on safe excavation of trial pits suggests a number of control measures such as the supervisor/logger should approach and stand at the opposite narrow end of the open pit to the machine, , arisings should be placed a minimum of one metre from the pit edge, and other controls. However, the industry, and associated industries who undertake not dissimilar construction activities, can still not agree on the approach to controlling the risk of working at height when trial pitting or even whether it is a significant risk in the first place.
The principal arguments for the requirement to approach open pits is to observe the formation of the ground and groundwater in situ, accurately measure stratum boundaries, water strikes, final depth and to take photographs. The industry could for example re-evaluate the necessity for photographs and the way they are taken, and whether they are used as anything else but proof the pit was dug. The question could also be asked as to ‘how accurate is accurate’ with respect to depths and is there a safer way to obtain this information. Some excavators can now determine depth of dig whilst excavating and perhaps providing depth markers on the excavator arm may be another alternative.
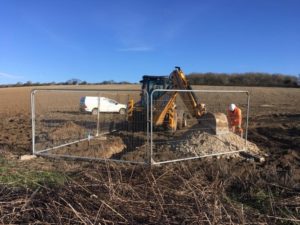
Figure 1 – Typical example of a machine excavated trial pit where the pit is logged from samples only
Employers must also consider the risk of injury from contact with plant and machinery. It is essential that the supervisor maintains good communication (both verbally and using agreed hand signals) with the machine operator at all times. Supervisors should be aware of the danger areas (red and amber zones) around the excavation and always stand in the yellow zone to maintain a clear line of sight.
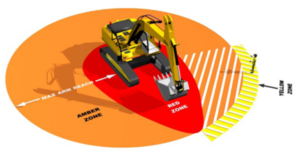
Figure 2 – An example of a safe working zone for mechanical excavation using a 3CX or 360 machine
It is not uncommon that the supervisor (often a graduate and in some cases with limited years of experience) will take on responsibilities for both the H&S and the technical goals of the trial pit investigation. In effect, they take on a role of supervisor, logger and banksman. In the construction industry, banksmen are operatives specifically trained to direct vehicle movement on or around site. How common is it that graduates or even experienced engineers are specifically trained in the role of a Banksman (or vehicle marshal), but are expected to fulfil such a role when directing plant and machinery around site. Therefore, the employer should provide training to allow the individual to carry out this role. This could be delivered through a formal Banksman course or might be better delivered as task specific in-house training which should include all aspects of safe trial pitting to help create competent people who can dynamically risk assess excavations.
But is trial pitting really or inherently a high-risk activity? Excavations are typically left open for only a very limited length of time and are backfilled as soon as the pit is completed in comparison to most construction industry excavations. In addition, there are no clear statistics from the HSE on injuries or fatalities from falls associated with trial pitting. These do occur in the wider construction industry, generally as a consequence of a collapse of the excavation which has been open for some length of time. As an industry we are all aware of the fatality to a Geologist in September 2008, however, statistics of injuries, accidents or near misses are not widely known and are often only communicated internally with site staff and not shared to the wider ground investigation community.
As an industry we must strive to continually improve the safety culture within ground investigation and trial pitting offers us all a chance to either look at current and future innovations to reduce the risk or find safer alternatives. There is a concern that if the industry does not obtain consensus that others may develop approaches which the industry may not find palatable both practically and commercially.
The current AGS document looks to provide practical guidance on trial pitting considering the current H&S guidance available, however, the Designer always has the choice to replace trial pits with boreholes or dynamic sampling holes which would, in many cases, provide similar design data.
The question remains, is trial pitting fit for purpose and the AGS would welcome views from the industry and will be sending out a short questionnaire to determine current industry practice and thoughts.
Article contributed by AGS Safety Working Group
Principal Authors – Adam Latimer, Ian Farmer Associates; Steve Everton, Jacobs and Julian Lovell, Equipe Group